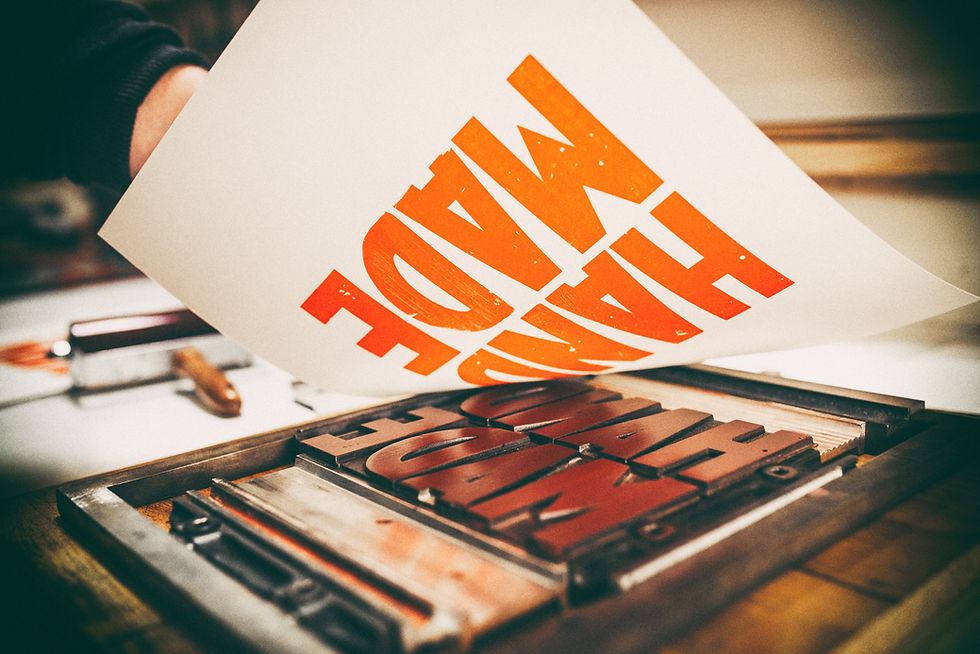
Each file you submit will undergo a 33-Print Check to make sure it meets print standard requirements, whether you’re in a rush to print or willing to wait for proof.
Before Printing: 13 MYPERFECTPACK- PRINTING Checkpoints
From our file prep checks to imposition, we run several checks to ensure that your project is printed accurately and professionally. (MYPERFECTPACK- PRINTING CHECKPOINT)
Verify artwork resolution. We see to it that the artwork meets the recommended resolution of at least 300 dpi. Low-resolution files will display obvious pixelation. However, uploading artwork with resolutions higher than 300 dpi will not improve print quality. It will only make the file size larger to process.
Confirm the artwork size. Uploaded artwork should have the same size as the order specs. If there is a difference, we will notify you so you can upload a new file with the same specs as your order.
Check bleed and safety zones. Important design elements should be within the safety zone to prevent them from being cut off after printing. If your artwork has a background, it should extend beyond the bleed to avoid the appearance of unwanted gaps after printing.
Verify that the artwork matches the order specs. This is a quick check to see if the artwork specifications are the same as the ones in your invoice.
Check and convert color mode. Images should be created in CMYK for accurate color printing. However, some files are created in RGB . In this case, we will convert the color mode for free to CMYK and check for major color shifts after conversion.
Make sure there is no unintentional color overlap. Overprinting is the process of printing one color over another. This makes the printed artwork look different from the one you designed. Checking for overprints ensures that the colors in your artwork do not mix with another color by mistake.
Check for after-printing requirements. If your order includes finishing (e.g., scoring, foiling, lamination, spot UV, or folding), our team will check your file to see if is included in the design.
Manually check the design for errors. Our team will make sure that your file is print-ready before it goes to printing. We will check colors, text placement, images, and transparencies. Spelling checks are excluded in this inspection.
Electronic checking. Our team will run another series of checks to fix any issue that may have been missed during the human inspection. Using preflight software, we can flag artwork issues and fix them. If the problem requires action, we will send the file back to you with our recommendations.
Ensure the right ink density. Laying too much ink on paper could lead to smudging. Using the right ink density allows printed designs to dry faster and prevent smearing.
Double-check order specifications. Our team will do a final human-led inspection to see if your order matches your file.
Check the order plating process. Our team will check that all marks (e.g., trim lines, color bars, etc.) are included before printing begins.
Inspect order output. We will print a small batch to check if the printed artwork quality is acceptable. This allows us to spot check errors before printing a large batch.
Printing and Finishing: 14 Checkpoints
During production, we go through a series of machine-run and human-led inspections of the printed product to catch errors and correct them.
Ensure all color levels are correct. As your project is printing, our team scans the printed artwork for color consistency. Using the closed-loop color system, we can make automatic adjustments to the colors and ensure that is true to your design.
Continuously inspect the product during printing. This helps ensures consistent quality and allows us to fix errors as we go.
Examine color density. We check each printed sheet for proper ink trapping, correct color breaks, and color consistency.
Compare the printed product to the original artwork for color fidelity. This ensures that colors are printed in the same hue and that all design elements are printed exactly the way you want them.
Ensure proper color registration. We check each color to ensure that they overlap precisely. This prevents images from looking blurred and having white spaces in areas where there should be color.
Double-check the correct positioning of elements. We make sure that all images, cuts, and scores are included in the printed product.
Check proper bleed. Before we print your project, we will run another check to see if there are any text or images that might be trimmed off.
Verify paper stock. Our team will check the weight, color, brightness, and texture to ensure that it is the same stock that you specified in your order.
Check the press sheet for inconsistencies. Our team will look at each image, text, and other design elements to make sure they are consistent with your design.
Review the printed proof to confirm that the artwork is printed correctly. We check for inconsistencies in pagination, text placement, font conversion, and other possible issues. We also inspect the printed product for missing elements and unintentional copy changes.
Check the quantities to print. We will compare order specifications against the actual copies printed.
Look for any imperfection and error in the printed sheet. Before we trim your product to its actual size, we will check the printed sheets for any blemishes, mottling, pinholes, and other flaws.
Verify all sheets are cut accurately. We will check and trim the bleeds before cutting your project to its final size.
Check product quality. Before moving to the next stage, your artwork will go through a human-led inspection to manually spot and fix errors, if there are any.
Quality Assurance & Shipping: 6 Checkpoints
The final quality inspection ensures that your printed product meets our printing standards and are shipped on time.
Run quality checks at every stage in production. Our trained Quality Assurance specialist will run several checks—from prepress to printing—to ensure that all products are up to standard.
Conduct final inspection before we ship your product. The final inspection will help us identify issues and allow us to fix them before we ship out the order.
Find the right packaging for the order. The boxes we use for delivery will depend on the number of products to ship. As an eco-friendly printing company, we use mostly recycled boxes to ship our products. This helps us pass on our savings from manufacturing and printing to our customers.
Verify the delivery address and shipping mode. We will double-check customer’s information and order specifications to ensure that the orders are correct and that they will arrive on time.
The shipping team will check the orders and sign shipping documents. To ensure accuracy, all shipping documents will be checked and signed off before shipping.
Provide tracking. Customers will know when their order ships without going to different shipping websites.
Your Order is Done: Satisfaction Guaranteed
Myperfectpack stand behind our products and our services. If you are not 100% satisfied with your print product, let us know and we will work with you on how to make it right.
Comments